Testing And Applying Innovative Heat-bending Techniques In Bamboo
By Leticia Matos Asilis | February 7, 2023 | Bamboo U Built Projects -
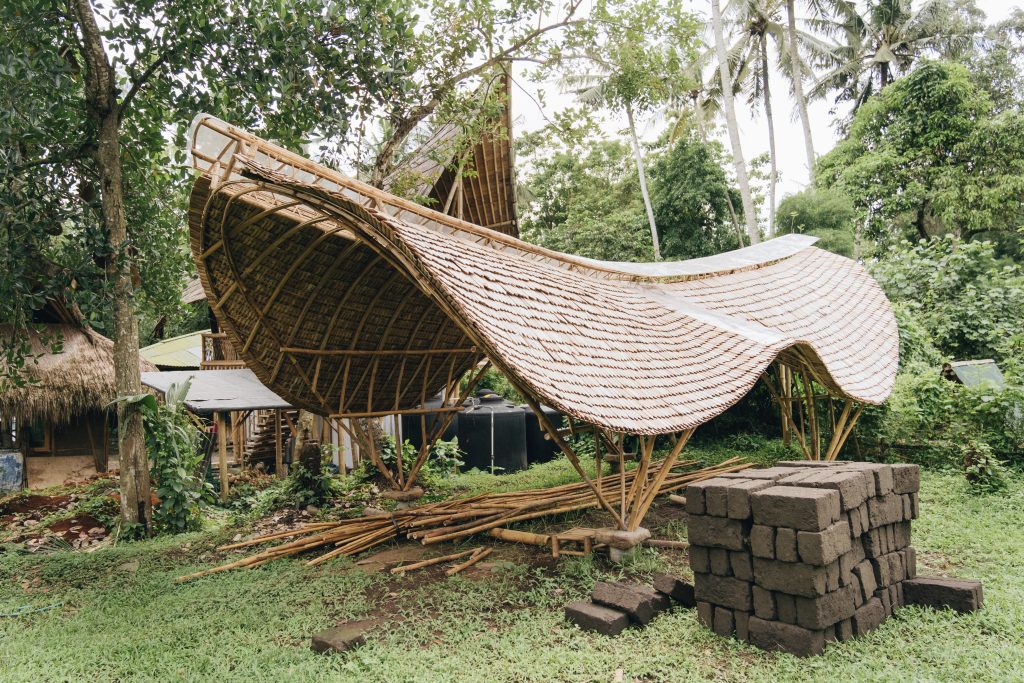
Join us in the process of building a curved structure using heat-bent bamboo!
Last August, the 11 Day Build and Design Course took place in Bali, where participants, with the guidance of the outstanding builder Jörg Stamm and our Bamboo U team, built a unique structure using heat-bent bamboo. The building, one of the first of its kind in Indonesia, uses the species Thyrsostachys siamensis, also known as “Bamboo Jakarta” or “Monastery Bamboo” for its strong and straight culms. This versatile species not only adds an ornamental touch but also serves as a barrier against wind and sound, making it ideal for lightweight structures.
Our Bamboo U team designed a small structure called the “Kitchen Prototype” where we combined laminated Petung (Dendrocalamus asper) splits and heat-bent Jakarta poles (Thyrsostachys siamensis). This innovative design was created as a test run for the upcoming Kul Kul Farm Restaurant and Kitchen, a very promising new restaurant that we are currently working on. By experimenting with heat-bent bamboo poles, we aim to understand the behavior of the structure on a smaller scale without overly compromising its structural integrity and strength. The Kitchen Prototype serves as a crucial step in advancing the use of heat-bending as a technique in bamboo construction.
In this article, we will walk you through the process of building a curved structure using heat-bent bamboo. The construction of this structure was divided into two parts, with one team preparing the arches at the heat-bending station, and another team building the prototype. Here is a brief overview of our project roadmap:
- Day 1: Heat Bending
- Day 2: Foundations and Main Structural Elements
- Day 3: Lidi Bundles and Laminated Split Arches
- Day 4: Other Structural Elements and Roofing
- Day 5: Lessons Learned and Next steps
In order to optimize the construction process during the course and make it more efficient, some tasks were previously done by our skilled carpenters. These tasks included:
- Pouring and leveling foundations.
- Pre-making laminated split arches.
- Assembling Thyrsostachys Siamensis bundles for the main arches (previously heat bent by our July 11 Day Course students).
- Setting up the scaffolding.
Day 1- Heat Bending
We familiarized ourselves with the project and its processes, as well as discussed our goals for the coming days. We were very excited to explore this new technique whilst continuing to discover alongside our students the wonderful potential of bamboo as a construction material. At the heat bending station, the team prepared some of the main arches for the structure. We witnessed how the bamboo changes color when exposed to high temperatures and with the help of a thermal camera, we were able to measure the exact temperature of the bamboo before reaching its breaking point. This was fascinating data that helped us continue with our experiment.
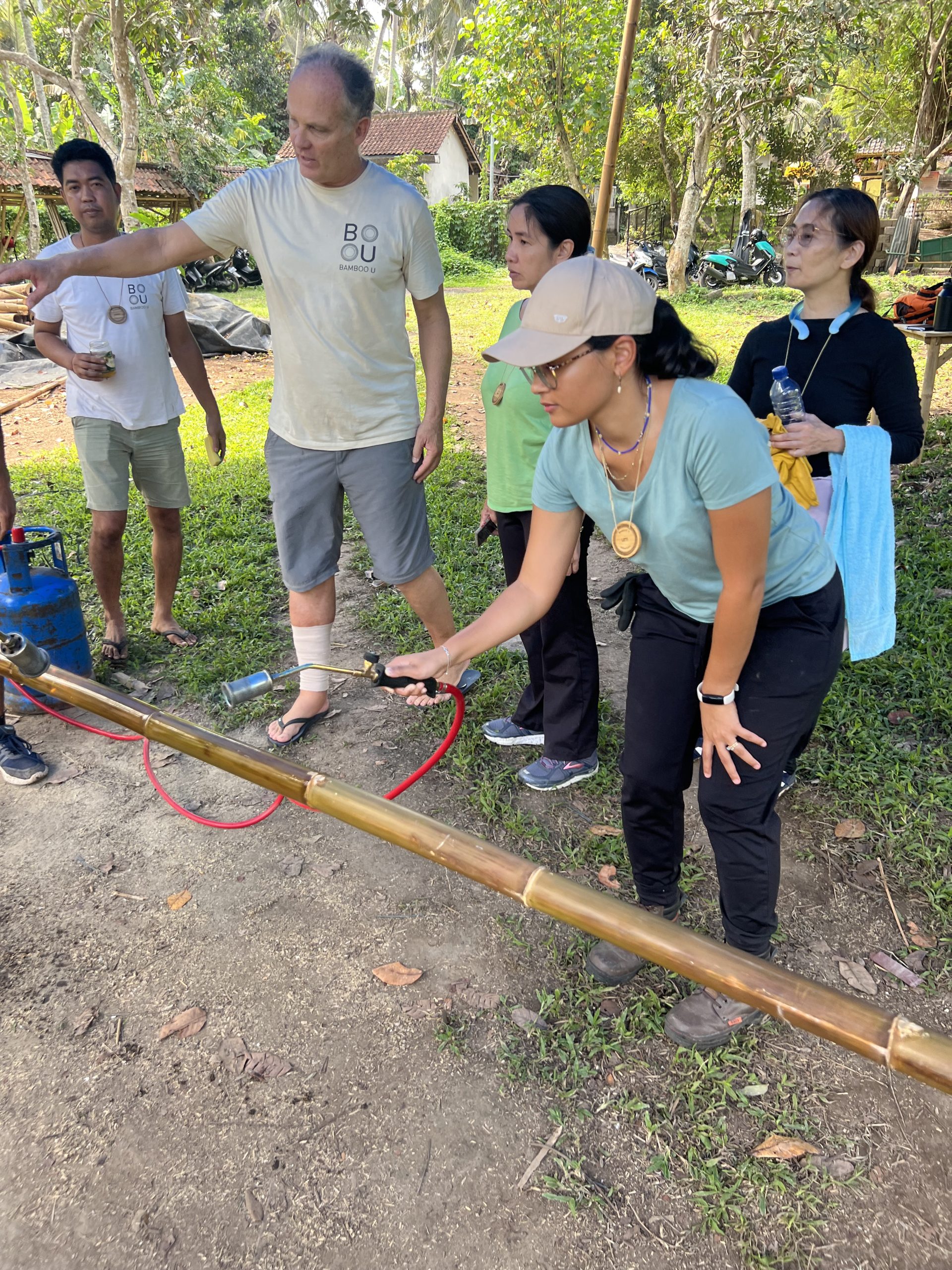
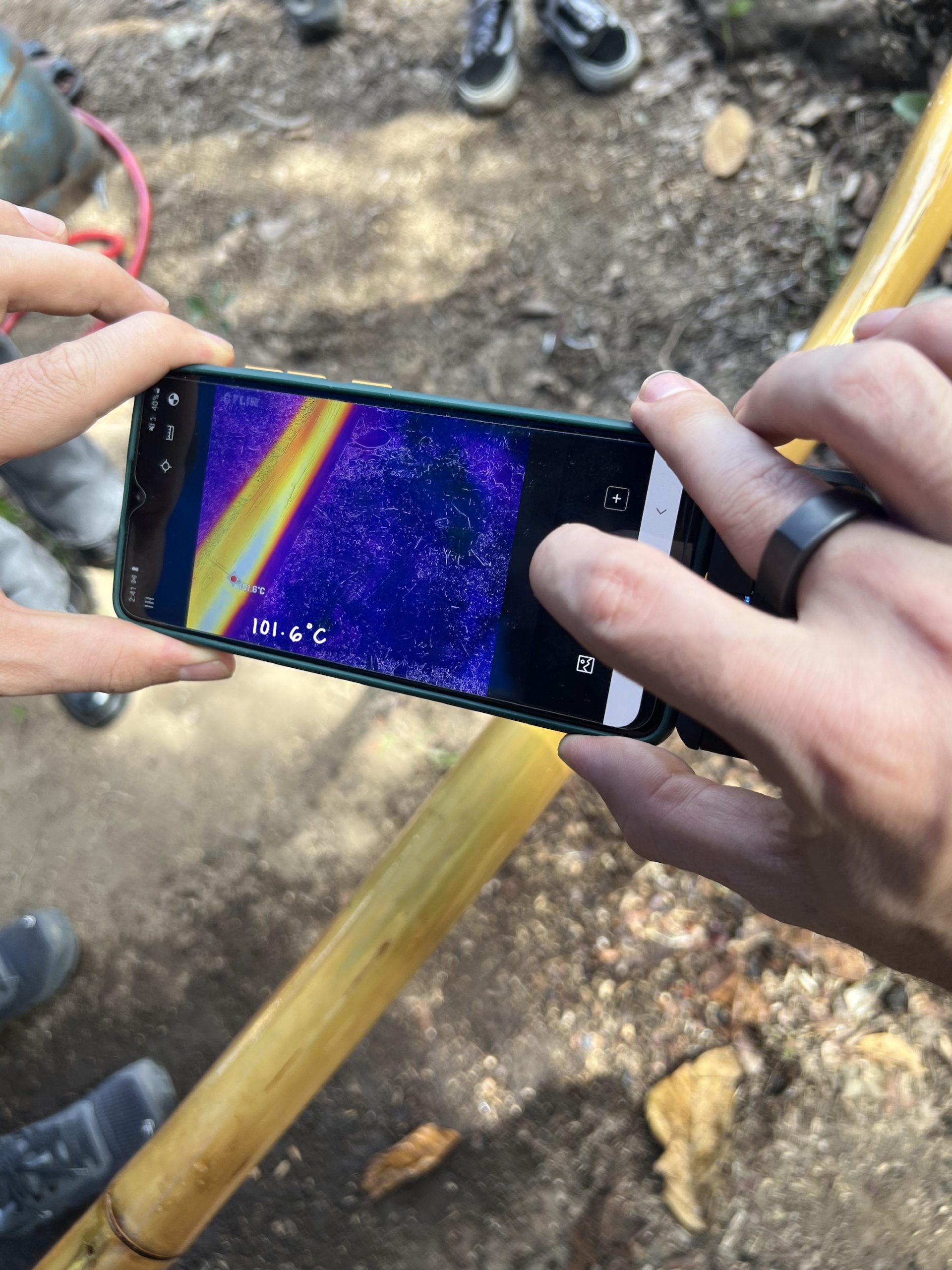
At the construction station, the team built the main skeleton of the project using the Thyrsostachys siamensis bundles. This day was all about learning and observation. Despite having an overall work plan, it was crucial to understanding the behavior of the structure to make decisions for the next steps.
By the end of the day, we successfully set the main structural heat-bent arches in place. It gave us a lot of satisfaction to start seeing how the building was taking shape!
Day 2 - Foundations and Main Structural Elements
On day two, we made significant progress. Orin instructed the team on how to mix epoxy resin and hardener to use as a strong adhesive. This mixture was applied to the rebars on the foundations, and later on, we punctured the nodes of the Thyrsostachys siamensis poles to fix the main arches of the structure, ensuring stability at the base. Jörg Stamm provided a valuable suggestion by proposing placing a large X on the main arches to locate the midpoint. This helped us obey the structure's geometry and bring us closer to the desired shape.
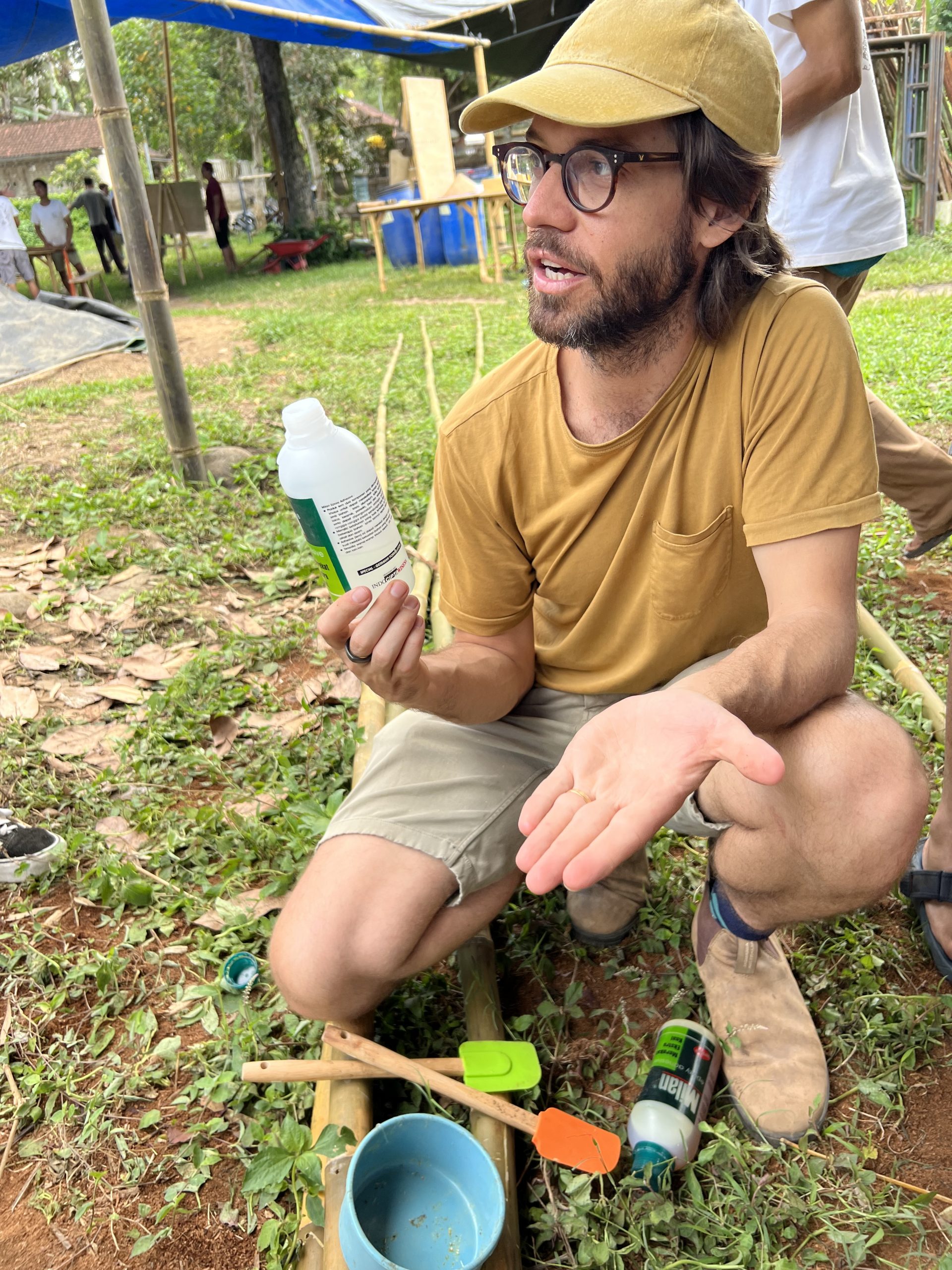
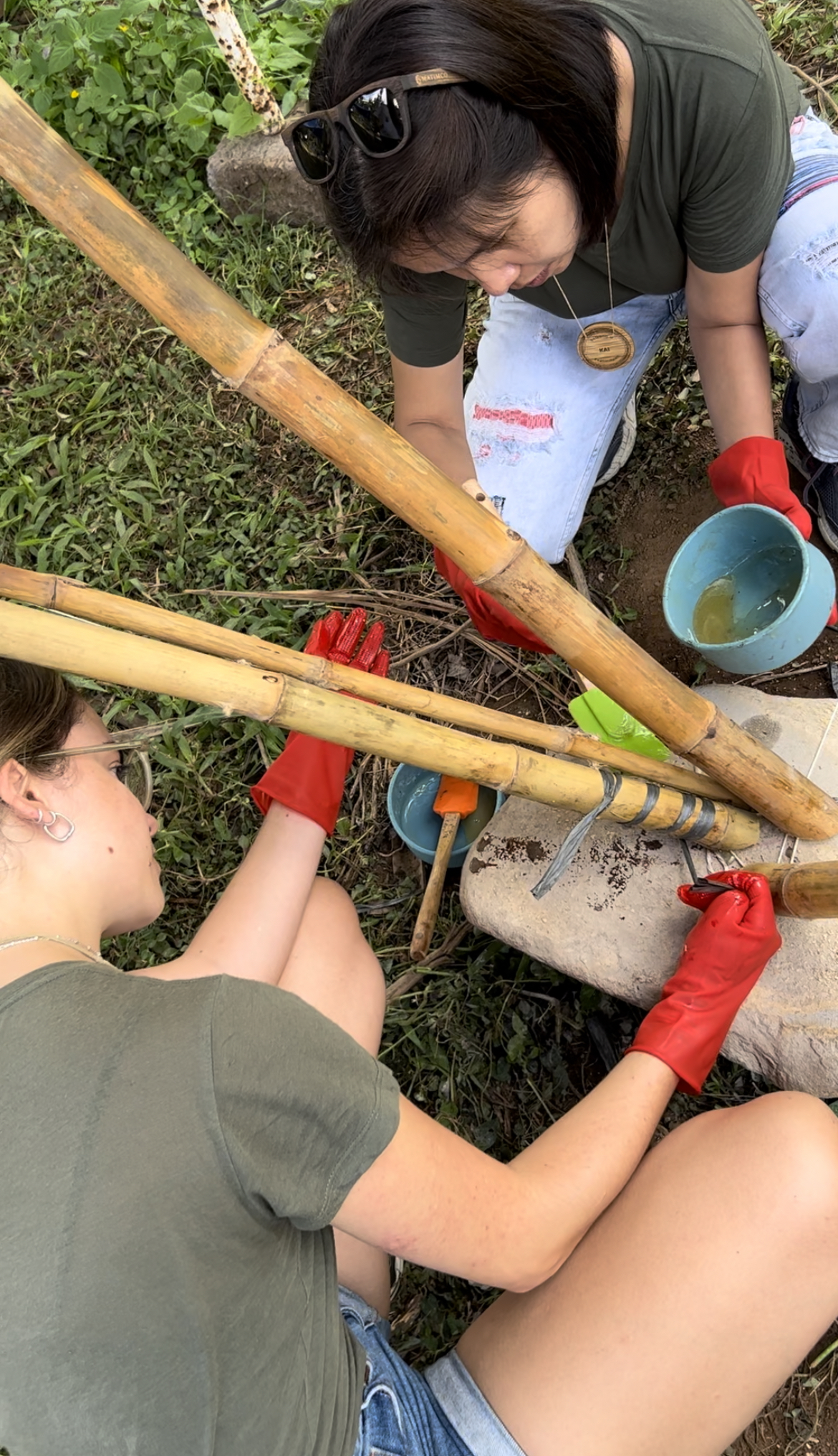
Another crucial step we began was installing the laminated split arches that eventually will work as support for the main structure, complementing the cross bracings. These secondary arches will facilitate the process of installing bamboo shingles or locally know as for the roofing.
Day 3 - Lidi Bundles and Laminated Split Arches
On this day we worked all together to assemble a 25-meter-long lidi bundle, which will serve as the roof's eave. Pak Wahoe and Pak Putu Abang taught us the lashing technique for the lidi bundle with metal wire first and then bamboo tali (Gigantochola apus) rope. We worked together to finish this bundle in a record time while the other part of the team fixed the laminated split arches to the structure. At the end of the day we installed the lidi bundle and shared exciting discoveries made at the heat bending station.
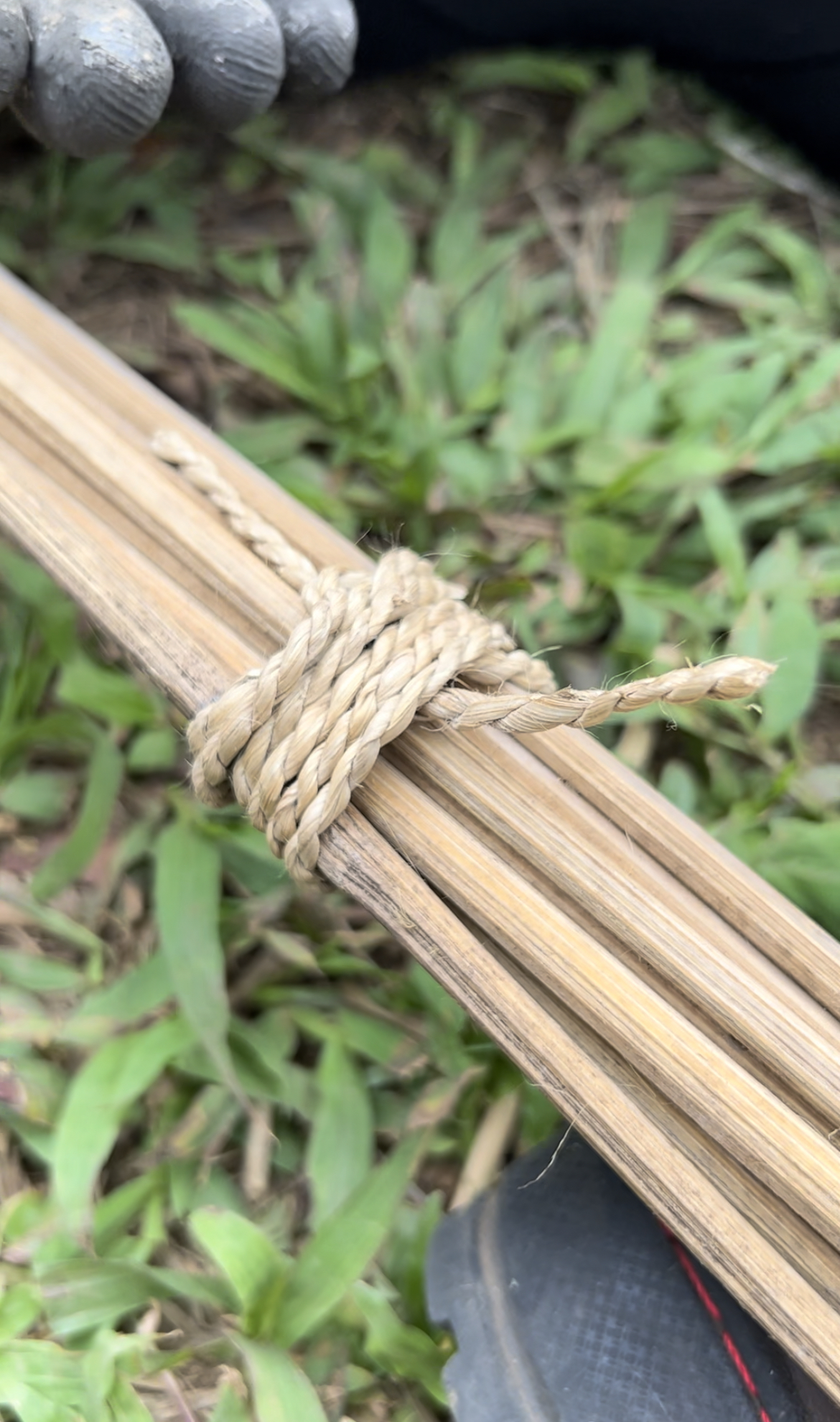
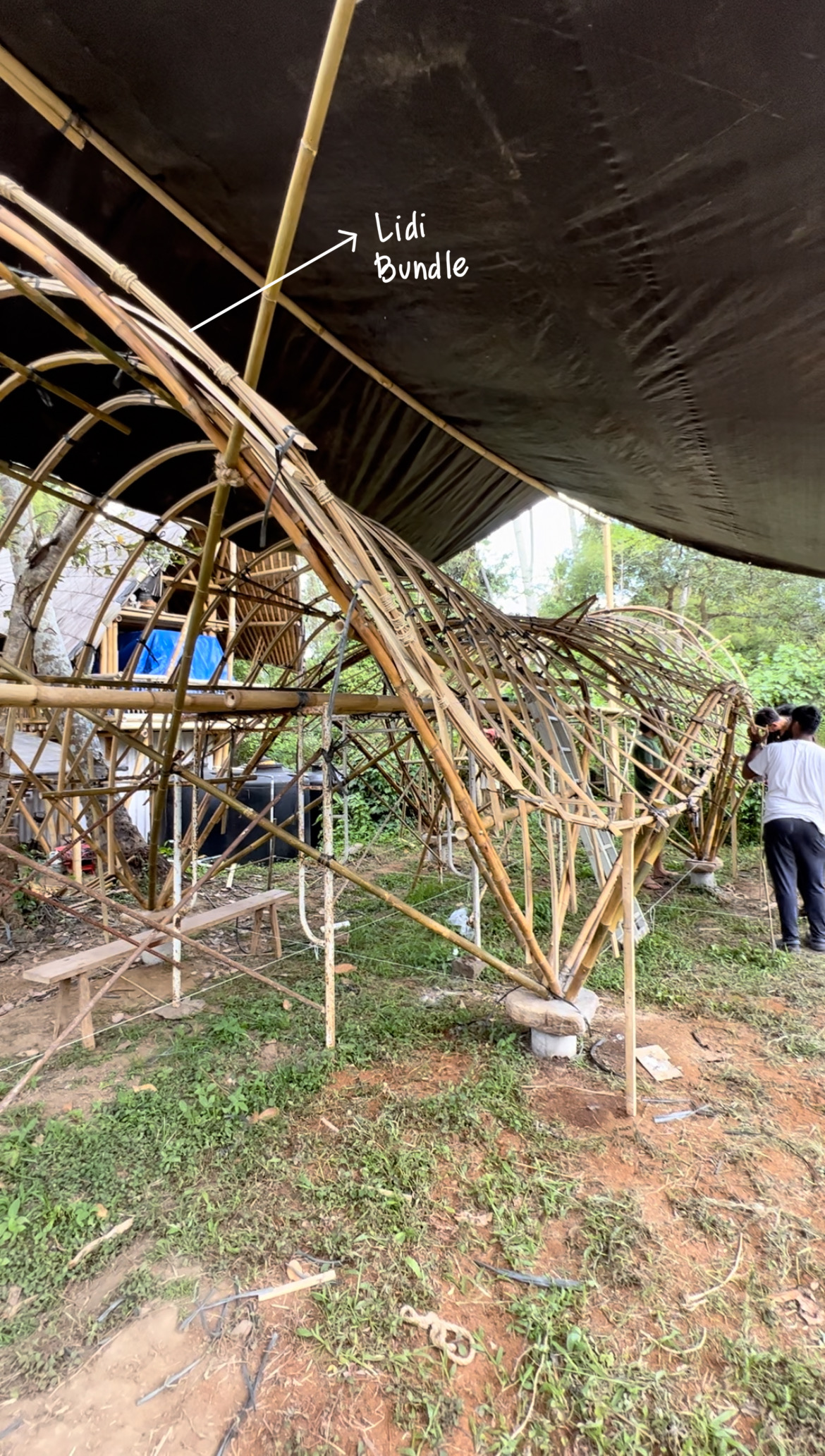
Day 4 - Other Structural Elements and Roofing
Day 4 was all about placing the horizontal battens perpendicular to the laminated split arches. Although it was a time-consuming task, the outcome was very rewarding. It was a repetitive process: drill the holes at an angle, place the bamboo pin with glue, and then cut the excess with a chisel and wood mallet. This sequence was repeated the whole day.
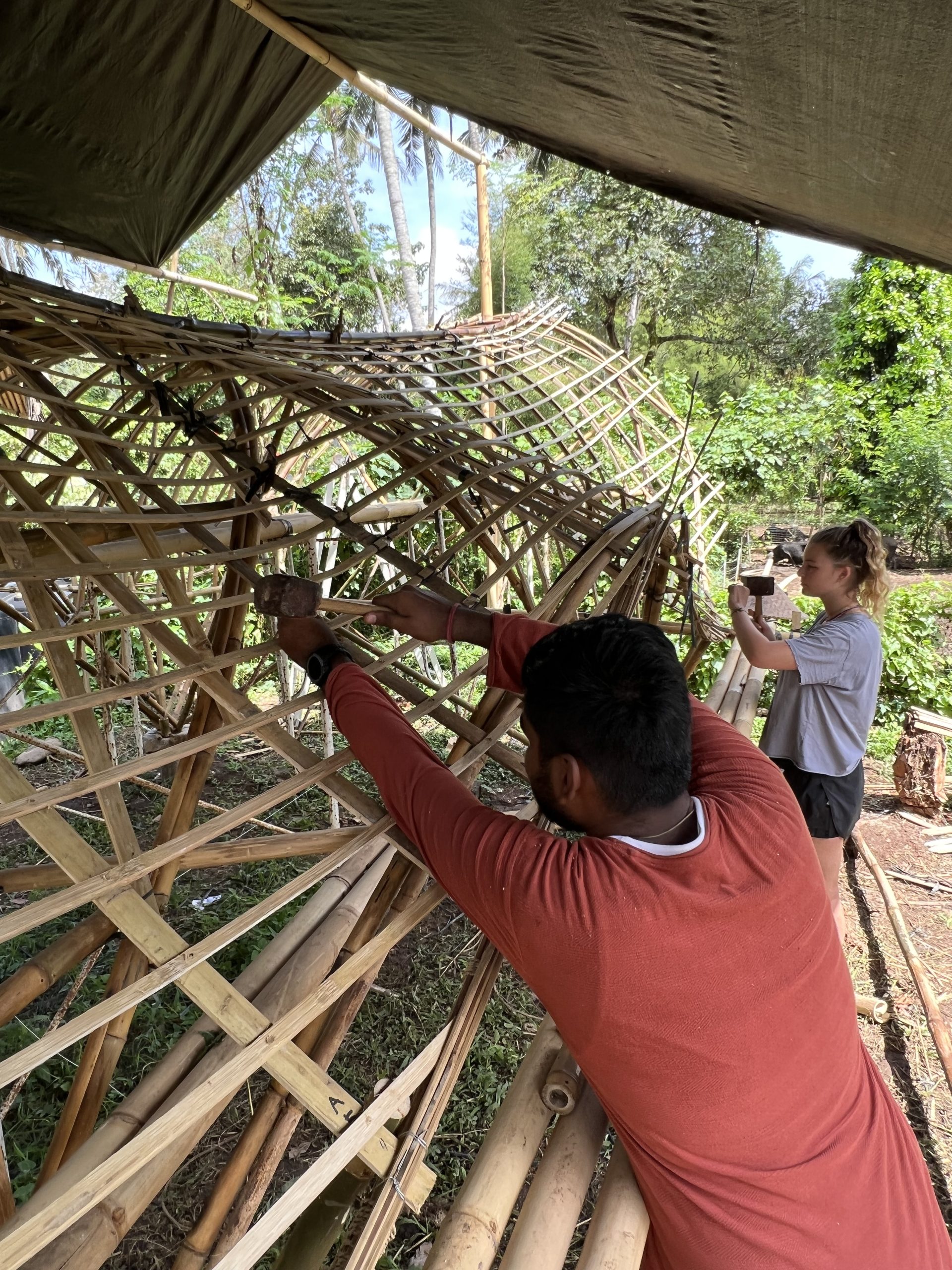
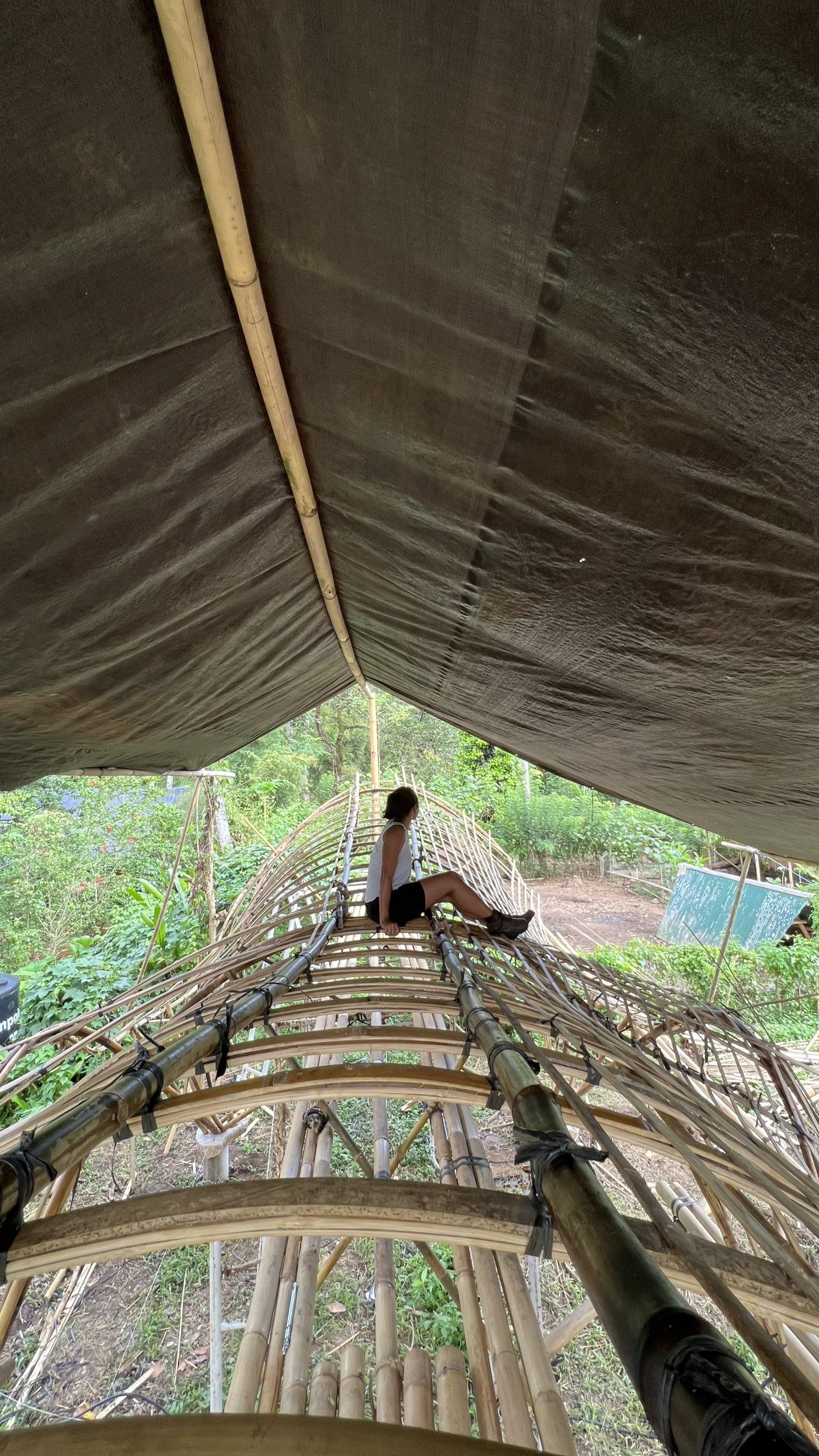
With the help of our carpenters, we fixed two heat-bent arches on the top of the structure which were later used as the base and support for the skylight. At the end of the day, our carpenters demonstrated the traditional Indonesian technique of Sirap roofing, showcasing how to install bamboo shingles. The assembly process of the shingles is quite interesting. They have a slot on the outside of the bamboo that attaches to the horizontal battens. They are installed upside down, with the silica facing upwards (convex side), to prevent water from flowing sideways and creating weak spots that could lead to leaks over time. Furthermore, the shingle acts as a natural pipe that causes the water to flow directly down
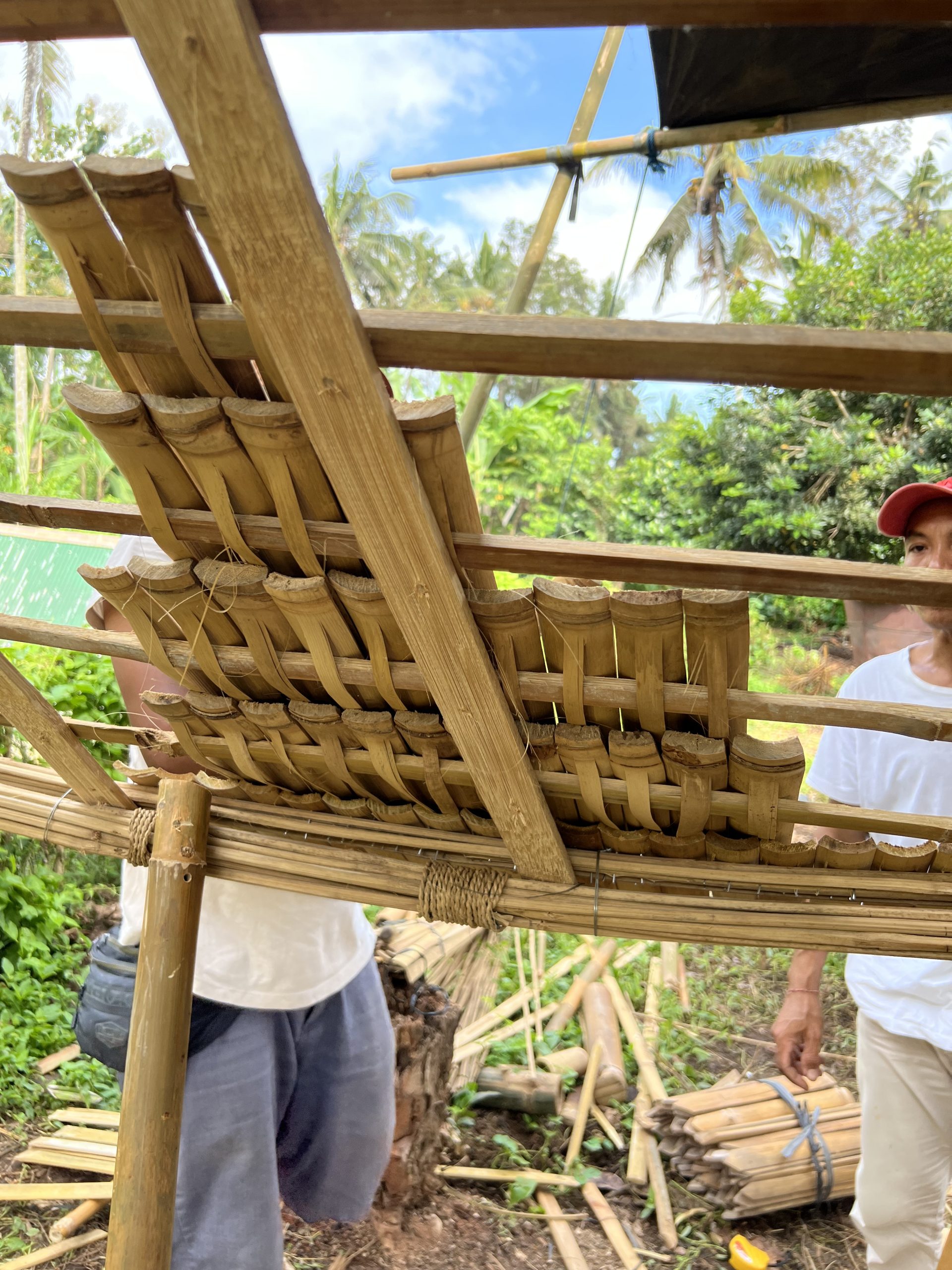
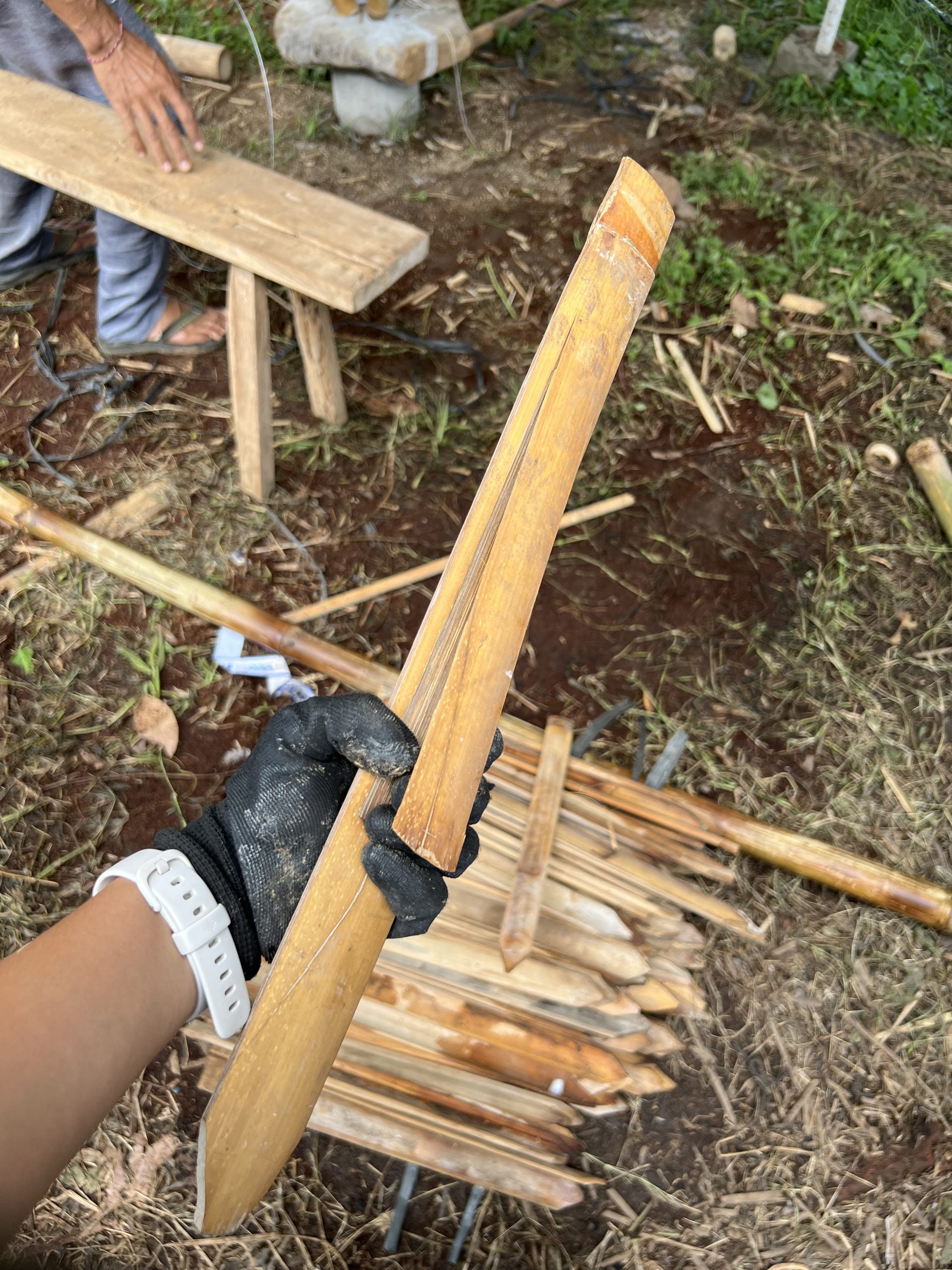
Day 5 - Lessons Learned and Next steps
On the fifth day of construction, students from other stations, expert facilitators, and the Bamboo U team gathered at the construction site for a brief meeting. We concluded with a review of the project and lessons learned.
After 11 days of teamwork, dedication, and hard work, our students gained hands-on experience in building lightweight structures with heat-bent bamboo. Our carpenters completed the skylight and Sirap roofing after the course. Upon completing the prototype, we noticed that the sirap roofing is causing an unexpected increase in weight on the structure. This highlights the importance of testing and prototyping, as it has allowed us to identify this issue before it became a problem in the actual building. To mitigate this, we will be incorporating additional supports in the final construction to ensure the structure can properly handle the weight of the roof.
The Bamboo U 11 Day Build & Design Course 2023's schedule is available. Bookings are filling up. We are ready to sail with you on your bamboo journey! We are looking forward to seeing you soon in Bali!

Leticia is an architect based in the Dominican Republic. She has always been passionate about the fusion of architecture and nature to create the perfect balance between organic spaces and modern requirements.
OCTOBER 10-21, 2025
The 11 Day Bamboo Build & Design Course in Bali
In 11 days, we'll show you how to build bamboo structures we’ll share all that it takes to build with nature.
Start Anytime
The Bamboo Harvesting Course
The Bamboo Harvesting Course is an online step-by-step training to harvest and care for your bamboo clumps to ensure their longevity and productivity. This maximizes the potential of this beautiful grass as a rapidly renewable resource.Whether you are an architect, builder, or sustainability enthusiast, this mini course will enable you to utilize this rapidly regenerative resource as a durable construction material.It will help remove any fear or doubt about the durability of bamboo and help you build reputable bamboo structures that stand the test of time!